Joseph Hummer
Biosystems Engineer
Qualified for a position in
Civil Engineering
Mechanical Engineering
Biological Engineering
Process Engineering
Environmental Engineering
Electrical/Computer Engineering
Willing to
Relocate
Travel on the job
Pursue additional training
Be Green Packaging
Engineering and Quality Intern
Summer of 2015
My experience as an intern at Be Green's manufacturing facility in Ridgeland, South Carolina was unique and challenging in a number of ways. The facility was new, and the process still required fine tuning and troubleshooting in order to work smoothly. Since I was one of the first interns at the facility, there was no existing structure or program to follow. I was also the second hire within the Engineering and Quality department at the facility, which gave me the opportunity to tackle some important projects and problems that the limited personel had not yet been able to address, some of which are shown below.
Despite some of the challenges presented during the summer, I very much enjoyed my experience and learned a lot about what it means to be an engineer in the process.
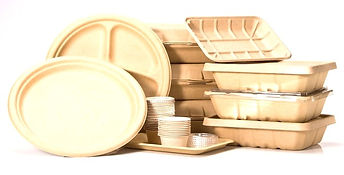

Main Projects
Work Photos
Shown below are a few photos to scroll through to help illustrate the types of problems I had to solve.
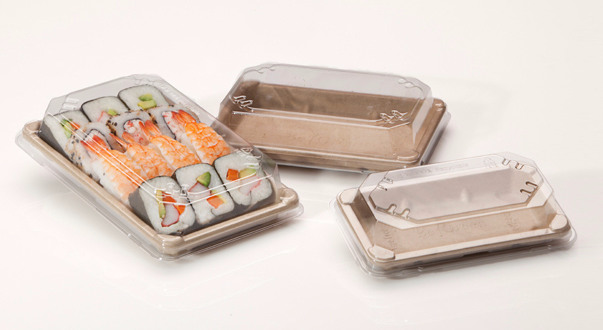
All products and processes in the facility were conformed to current health and safety standards. The projects I worked on often came in contact with the pulp and thus had to be made of FDA compliant materials. This often drove the final design of the process modifications made throughout the summer.

Many of the machines in the facility were built, calibrated, and operated using the metric system while many of the modifications made were often in customary units. Conversions were a necessary part of daily problem solving and precision was essential.

As I looked for ways to improve the efficiency and safety of the facility, I felt that there was a need for better spill control and containment. After considering many methods of accomplishing this goal, I eventually designed and built a mobile spill station that contained all manners of absorbents and cleaning implements.
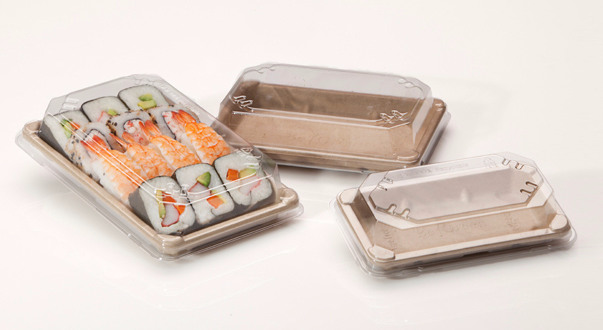
All products and processes in the facility were conformed to current health and safety standards. The projects I worked on often came in contact with the pulp and thus had to be made of FDA compliant materials. This often drove the final design of the process modifications made throughout the summer.
Flange Quality Improvement
Improving the edges of our product was determined to be a priority for the satisfaction of our customers and promotion of sales during my internship. Most of the experimental setups and modifications were entrusted to my care. After taking hundreds of samples from several different setups, a few contributing factors were found and noticeable improvements were made. There was still much to be done when I left, but significant reduction in scrapped product and multiple comments on the improvements have lead me to regard this project as a success. Additional details can be viewed here.
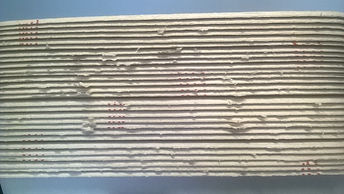

Pulp pH Regulation
About three weeks into my time at Be Green, the product began repeatedly failing certain oil and water resistance tests without any changes on the production line. After pursuing several theories, it was finally determined that the cause was a significant rise in incoming water pH. I was then tasked with finding the most reliable method of dosing the pulp with acetic acid to counteract the high pH of the water. I experimented with dosing intervals and locations in the process, relying on the process operators to try new methods and record data. With their help, I was able to find the most convenient dosing intervals and proportions, establish standard operation procedures for acid handling, and begin and even develop correlations between pH and product performance. At the end of the summer I was able to make reccomendations for the installation of an automatic pH adjustment system, which would allow the factory to put this issue to rest.

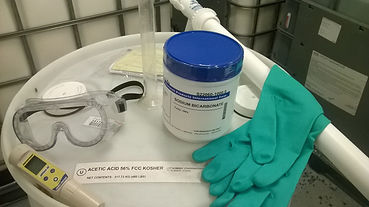